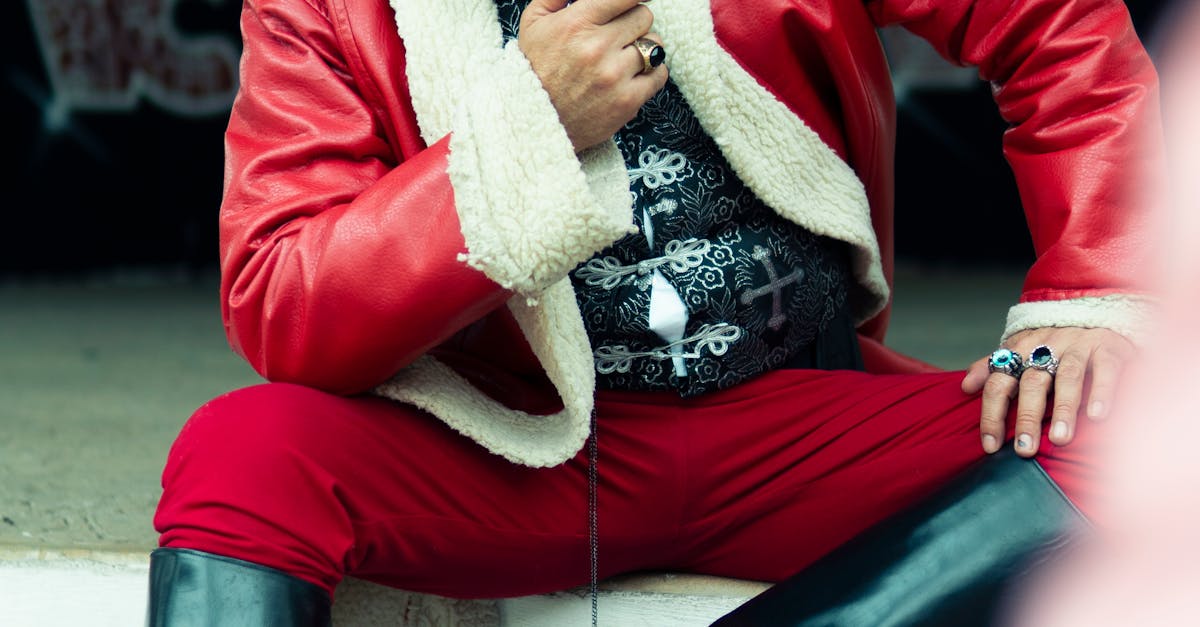
Table Of Contents
The Length and Condition of Pipes
The length and condition of the pipes play a crucial role in determining the cost of pipe relining. Longer pipes often necessitate more materials and labour, which directly influences the overall expense. Additionally, pipes in poor condition may require extensive preparation before relining can take place, increasing the time and resources needed for the job. Each unique situation must be assessed, as this evaluation will significantly affect the final pricing of the relining process.
Furthermore, the specific material and structural integrity of the existing pipes impact the complexity of the relining procedure. Older pipes or those with significant structural damage may require special attention or customised solutions, further driving up costs. As such, understanding the condition and configuration of the piping is essential for accurate budgeting when considering pipe relining.
Evaluating the Extent of Damage and Its Costs
The extent of damage within a pipe directly influences the overall cost of repair. Inspectors often use advanced technologies, such as cameras, to accurately assess the condition of the pipes. This assessment reveals issues like cracks, blockages, or corrosion. Each type of damage requires a different approach, with more severe issues necessitating additional materials or labour for effective pipe relining. Such thorough evaluations are essential to determine the best course of action and ensure the longevity of the repair.
Cost estimates for pipe relining projects can vary significantly based on the initial assessment. If the damage is localized, repairs may be less expensive, while widespread issues increase the complexity of the project. Factors such as accessibility and the materials needed for relining also play a crucial role in determining the final price. Transparency in pricing becomes vital, as customers need a clear understanding of the potential costs involved based on the severity of the damage.
Permits and Regulatory Considerations
Before embarking on a pipe relining project, property owners often face a maze of regulatory requirements that can impact the overall cost. Local councils typically mandate permits for significant underground work. Compliance with these regulations ensures that the project meets safety and environmental standards, but it can add both time and expense to the pipe relining process.
Navigating these legal requirements often involves additional fees and inspections that may not be immediately apparent at the outset. Depending on the location and complexity of the job, these costs can quickly accumulate. Understanding the specific regulations applicable to pipe relining in one’s area helps property owners prepare for these expenses and avoid potential delays during the project.
Navigating Legal Requirements and Associated Costs
Before commencing any pipe relining project, homeowners often need to navigate a maze of legal requirements and permits. Many local councils establish regulations to ensure that underground work adheres to safety and environmental standards. This means obtaining the necessary approvals can incur additional costs due to application fees and potential consultation with professionals knowledgeable about these regulations.
Furthermore, failing to secure the appropriate permits can lead to penalties or costly rework. Compliance with the various legislative frameworks is crucial to avoid setbacks during the relining process. As a result, the overall expense of pipe relining can increase significantly when factoring in these legal considerations that must be dealt with before any physical work begins.
Comparison with Traditional Repair Methods
Traditional repair methods often involve extensive excavation to access and replace damaged pipes. This process is not only time-consuming but also disruptive to the surrounding landscape and infrastructure. The costs associated with excavation can escalate due to the need for restoration once the work is completed. In contrast, pipe relining is less invasive, often requiring minimal digging. This method allows for repairs to be completed more quickly and efficiently, reducing overall labour costs.
While initial costs for pipe relining might seem higher, it is essential to consider the long-term benefits. The durability of relined pipes can lead to fewer repairs over time compared to traditional methods. Additionally, the streamlined process associated with pipe relining can reduce downtime for businesses or households. As property owners weigh their options, understanding the differences in cost and impact is crucial for making an informed decision.
Cost Differences Between Relining and Excavation
Pipe relining presents a modern alternative to traditional excavation methods when addressing damaged pipelines. While traditional repairs often involve significant digging and disruption, which increases labour and restoration costs, pipe relining is less invasive. This method primarily focuses on the internal surface of existing pipes, reducing the need for extensive external work. Overall, the efficiency of pipe relining can lead to cost savings, particularly in urban areas where access to utilities and roadways poses additional challenges.
Despite the advantages of pipe relining, initial costs may still seem high compared to traditional methods. Factors like advanced materials, specialised equipment, and skilled technicians contribute to these expenses. However, when considering the long-term benefits, including reduced likelihood of future repairs and minimal disturbance to the surrounding environment, many property owners find pipe relining to be a financially viable option. This technique also limits downtime, which can be crucial for commercial properties needing to maintain operational capabilities.
FAQS
What factors contribute to the high cost of pipe relining?
The cost of pipe relining is influenced by several factors, including the length and condition of the pipes, the extent of damage, required permits and regulatory considerations, and the complexity of the job compared to traditional repair methods.
How does the condition of pipes affect relining costs?
If the pipes are in poor condition or have significant damage, additional preparation work may be necessary before relining, which can increase overall costs. Evaluating the extent of the damage is crucial for determining the final price.
Are permits necessary for pipe relining, and do they add to the costs?
Yes, permits are often required for pipe relining to ensure compliance with local regulations. The costs associated with obtaining these permits can increase the overall expense of the project.
How does pipe relining compare to traditional pipe repair methods in terms of cost?
While pipe relining may seem more expensive upfront, it can be more cost-effective in the long run compared to traditional excavation methods due to reduced labour costs and minimal disruption to landscaping and infrastructure.
Is there any way to reduce the costs associated with pipe relining?
To potentially lower costs, homeowners can consider getting multiple quotes from different contractors, ensuring their pipes are well-maintained, and addressing minor issues before they escalate into larger problems that require relining.